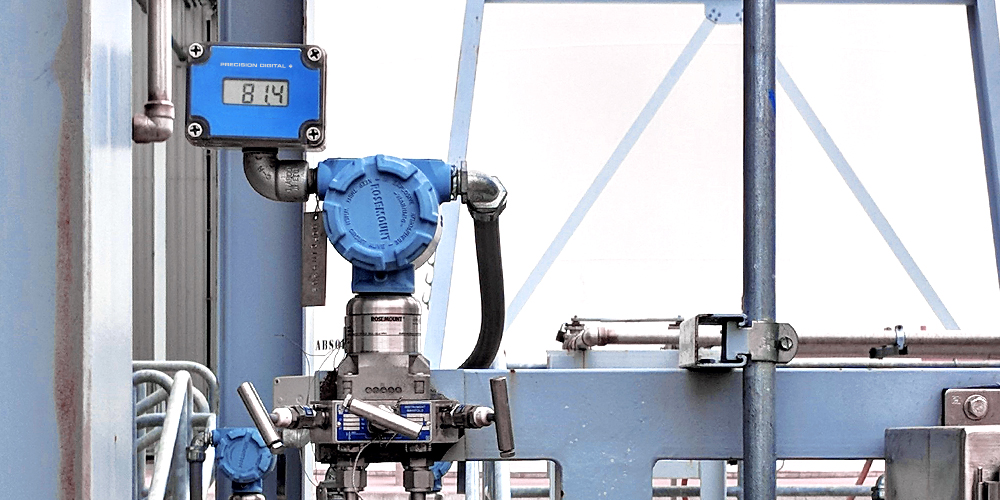
Using a loop powered meter is often a great choice for displaying a single process variable because it is easy to integrate into existing 4-20 mA current loops, does not require local power, and is a low-cost option compared to line powered meters. In addition, loop powered meters require only two wiring connections. This simplifies wiring significantly and reduces wiring costs.
It is easy to add a loop powered meter to an existing process control system using a 4-20 mA current signal to transmit a process variable. Simply break the 4-20 mA signal loop in the desired location and wire in the loop powered meter. In the example below, Figure 1 shows a typical 4-20 mA loop in which a 24 VDC power supply powers a 4-20 mA transmitter. Often, these transmitters lack a legible display or are installed in difficult to reach spaces such as inside a sump or on top of large tank. This is why such applications frequently install a remote display, such as a loop powered meter, in a convenient place to quickly and safely access process information. Figure 2 demonstrates this solution. A loop powered meter has been wired into the 4-20 mA loop, and because a loop powered meter derives all its power from the current loop, no external power is required. This is important for remote installations where no additional power is readily available, especially in a hazardous area where running power lines can be costly.
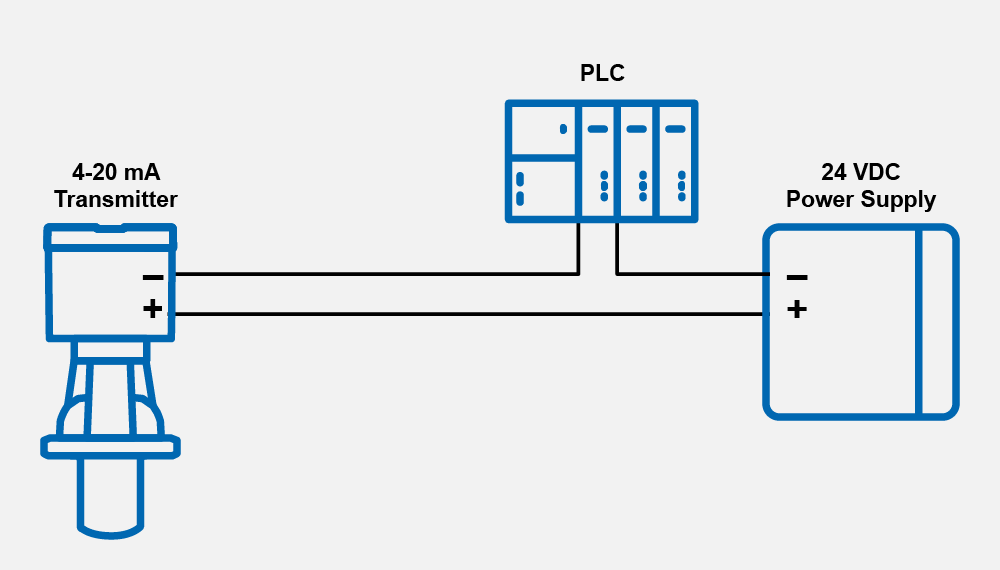
Figure 1. Typical loop in which a 24 VDC power supply powers a 4-20 mA transmitter and PLC
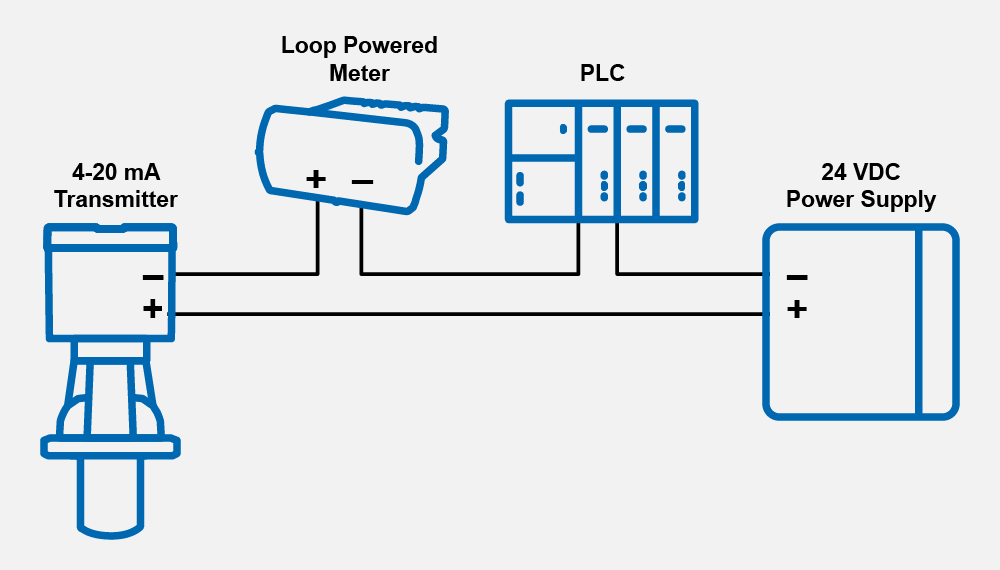
Figure 2. A loop powered meter added to a 4-20 mA transmitter loop
Generally, using a loop powered meter provides a simple solution that can be easily integrated into an existing 4-20 mA current loop to display a single process variable from a transmitter without needing additional power supplies, modifying existing equipment or wiring schemes, or running up excessive installation costs.
Benefits of using a loop powered meter
- Integrates easily into existing process control systems
- Derives its power from the loop it is connected to, therefore it does not require local power
- Requires only two wire connections, making it easy to install and reduces wiring costs
- It is a Low-cost option compared to line powered meters
- Delivers a simple display solution for a 4-20 mA transmitter
- Provides more hazardous area approvals options
When should I use a loop powered meter?
A loop powered meter is typically used in simple process control applications where the display of a single process variable is needed, the process variable is being transmitted by a 4-20 mA current loop, and no additional power is available. A loop powered meter can be easily integrated into an existing loop, such as a 4-20 mA loop, which supplies the loop powered meter with both the process signal and all the power it needs to function, therefore no separate power source is required.
Loop powered meters are also a great choice for hazardous area applications because they are often agency approved as intrinsically safe (I.S.) and nonincendive (N.I.). Both ratings require that devices consume very little power so that they cannot cause combustion under normal operating or fault conditions, respectively. Because power consumption in loop powered meters is inherently low, they are great candidates for these hazardous area approvals.
The low power nature of a loop powered meter can have its limitations as discussed in the fundamentals of loop powered devices. However, not all loop powered devices are created equal as some can offer advanced display and control features. Overall, a loop powered meter is a smart solution for displaying a single process variable from any 4-20 mA transmitter in safe or hazardous areas (with the right approvals).
What powers a loop powered meter?
Loop powered meters connected to a 4-20 mA current loop get their power from the loop itself. The current flowing through the loop powers a loop powered meter as well as provides it with the process variable signal the meter will display. Therefore, loop powered meters have no additional power requirements. This makes them ideal candidates for applications where no power is readily available.
Loop powered meters are also great for hazardous areas that require instruments with very low power consumption, provided they carry intrinsically safe and/or nonincendive agency approvals.
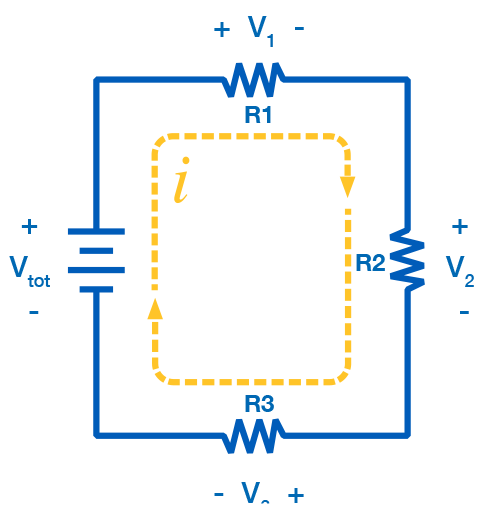
Figure 3. Basic current loop
Related: Loop vs Line Power
What is the difference between a loop powered meter and a line powered meter?
The main difference between a loop powered meter and a line powered meter is the number of wiring connections required to both power the meter and receive a process signal. Each type of meter offers unique advantages and limitations. Therefore, it is important to consider the different set of capabilities loop vs line powered meters have to offer.
A loop powered meter is connected to a 4-20 mA current loop using two wires. This is why they are also known as a two-wire device. Loop powered meters get their power from the 4-20 mA loop from which they are connected to and receiving a process signal. This makes them an ideal option for integrating into existing loops. The 4-20 mA current loop is one of the most used process signals in the process control industry because it is a very reliable means of conveying process information.
Loop powered meters use very little power and as a result are great candidates for hazardous area approvals. Loop powered meters typically feature LCD screens and limited functionality. Although in recent years loop powered meters with advanced display and control capabilities are becoming available and redefining the standard of what is expected from a loop powered device.
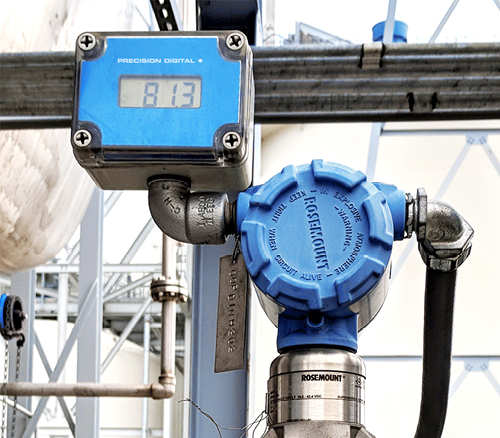
Loop powered meter being powered by and receieving a process signal from a 4-20 mA transmitter loop.
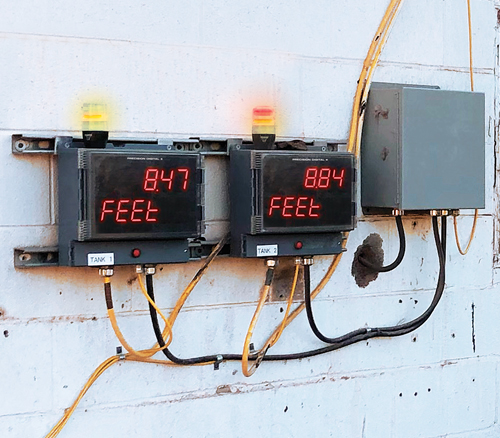
Line powered meters with LED displays powering light/horns used to indicate alarm conditions.
On the other hand, a line powered meter requires power from an external power supply that is separate, but not necessarily isolated, from the process signal loop it is connected to. Therefore, they need additional wiring to accommodate this power source. Line powered meters may also be referred to as three or four-wire devices, depending on the number of wiring connections used.
Line powered meters generally have more features and functionality that demand higher power consumption, therefore, they cannot be loop powered. These features may include bright LED displays, multiple relays and analog outputs, serial communications, and isolated 24 VDC transmitter power supplies that can be used to power the 4-20 mA transmitter. Some line powered meters have an internal power supply to power devices including the 4-20 mA transmitter they are receiving the signal from, alarm lights, and horns.
As a result, line powered meters are best suited for new installations. Line powered meters may also be approved for hazardous areas; however, they are often housed inside of an explosion-proof enclosure.
Loop Powered Meters and Line Powered Meters Comparison
Below is a quick overview of the defining characteristics and the differences between loop powered meters and line powered meters.
Loop Powered Meters | Line Powered Meters | |
Power Source | Loop | External power supply |
Wiring | Two-wire connections | Three or four wire connections |
Features/Functionality | Limited | Relays, analog outputs, retransmission, serial communications |
Screen Type | LCD | LED |
Power the Transmitter | No | Yes |
Cost | Low | High |
Hazardous Area Approvals | More Options | Limited Options |
Best for | Existing Loops | New Loops |
What is a 4-20 mA current loop?
A 4-20 mA current loop is a common signal used in the process industry. The signal transmits information with a variable current, from 4 mA to 20 mA. It is a DC signal, typically driven by a 24 VDC power supply. The 4-20 mA signal wire loop connects electronic devices in series, and loops a 4-20 mA current signal, driven by a DC power supply, through each device connected to the loop. A typical 4-20 mA current loop consists of a DC power supply, a 4-20 mA transmitter, and a receiver such as a loop powered meter or display. In a common 4-20 mA current loop, the transmitter produces a 4-20 mA current signal, the signal is pushed through the loop by the DC supply to the device receiving the signal and then back the transmitter.
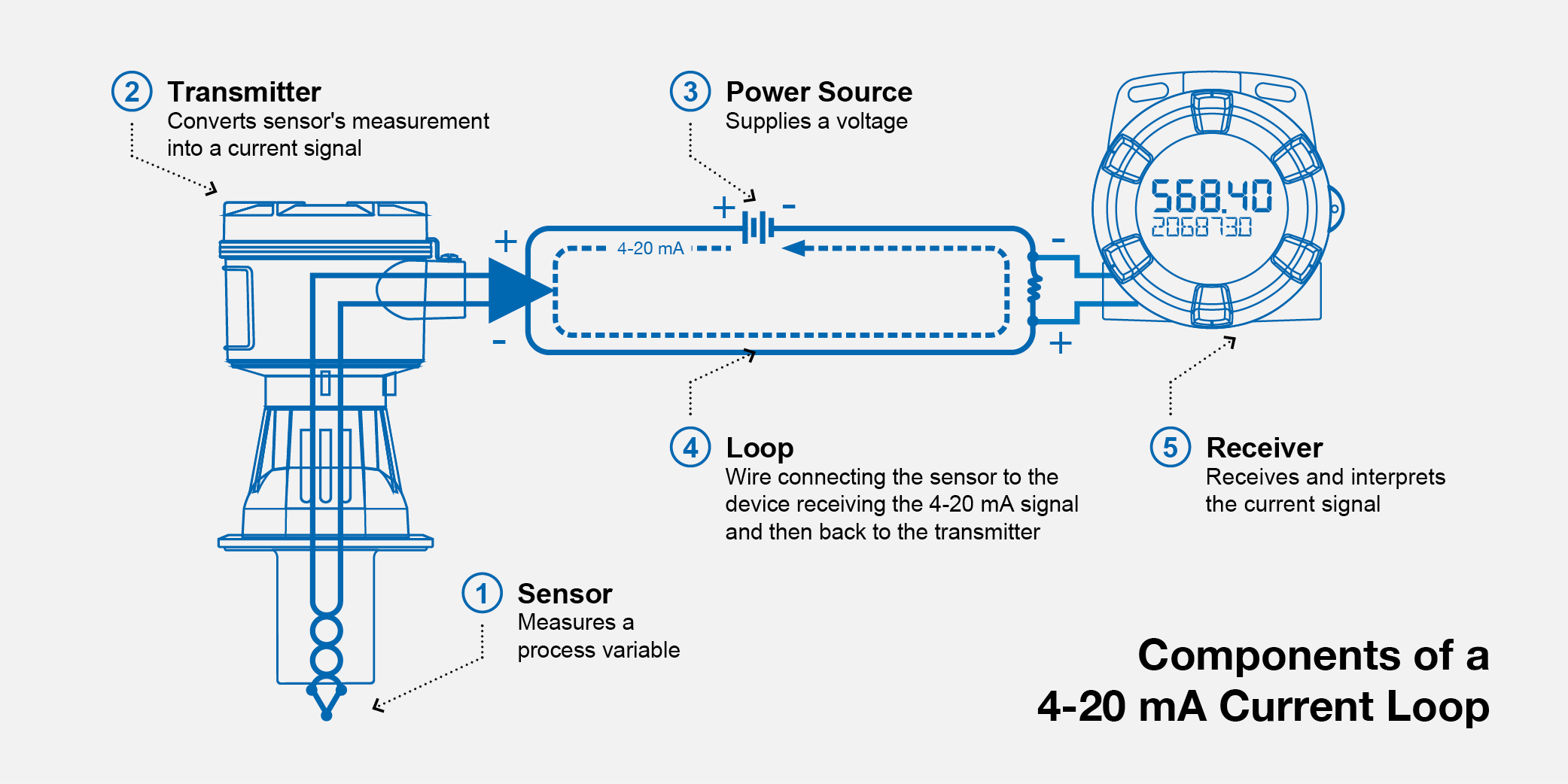
Figure 4. Components of a 4-20 mA Current Loop
The 4-20 mA current loop is the prevailing process control signal in many industries because it is an ideal method of transferring process information as current does not degrade nor change as it travels from transmitter to receiver across long wires, it is easy to identify a failed system (it has a non-zero current low range), it is more noise resistant that some other process signals, and it is often much simpler and more cost-effective than using serial communications protocols.
Related: Why a 0 mA Signal is Not Practical
You may be interested in
PD685 Intrinsically Safe IP67 Loop-Powered Meter
An easy to use, loop-powered indicator, certified by CSA, ATEX and IECEx as intrinsically safe for use in gas and dust hazardous areas worldwide.
PD6600 Loop Leader Loop-Powered I.S. & N.I. Process Meter
UL and C-UL Listed as intrinsically safe and nonincendive and ATEX and IECEx Certified for Intrinsic Safety in Hazardous Areas
PD765 Trident Process & Temperature Digital Panel Meter
One of the most versatile digital panel meters on the market that can satisfy a wide variety of process and temperature applications.