Ground Loops & Non-Isolated Commons
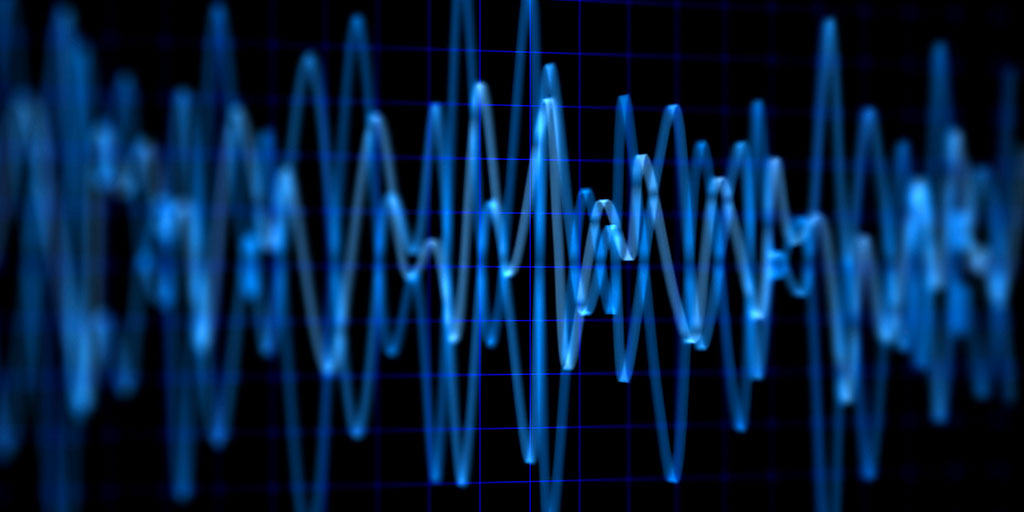
Signal noise in an industrial environment has the ability to cause havoc with process control systems. This electrical noise can inject itself onto analog or digital signals and fool control equipment into thinking the process variable is different from what it actually is. This miscommunication between process control equipment, as with all kinds of miscommunication, can lead to any number of unforeseen, unintended consequences. As any electrical engineer will tell you, no system can continue to function properly without proper communication.
No industrial facility is going to ever be 100% free of electrical noise. The low levels of noise present in most plants is typically not enough to cause a problem. It is when the signal-to-noise ratio gets to unmanageable levels that it becomes a problem. Hardware and software solutions are available to help combat signal noise in particularly noisy environments, including noise filter settings that may be

available in existing equipment already installed but inadequately utilized. Buying expensive new equipment in order to filter noise or isolate signals should, in most cases, be unnecessary if proper planning and installation practices are adhered to in the first place. Knowing what signal noise is, what causes it, and how to prevent it from interfering with signal networks should provide the right arsenal of tools needed to keep communication flowing.
DEFINING SIGNAL NOISE
Signal noise, in its most basic sense, is any unwanted interference that degrades a communication signal. Signal noise can interfere with both analog and digital signals; however, the amount of noise necessary to affect a digital signal is much higher. This is because digital signals communicate using a set of discrete electrical pulses to convey digital “bits.” As can be seen in Figure 1, those electrical pulses would require a lot of noise in order to be confused with one another.
Conversely, analog signals represent an infinite range of possible values using an established range, such as 4-20 mA or 0-10 V. In this case, any unwanted voltage or current spikes will cause a fluctuation in the message being communicated. Minuscule variations along analog signals, on the order of millivolts or microamps, typically do not result in a significant (or even perceptible) discrepancy. High levels of electrical noise, however, can produce large variations and therefore lead to substantial discrepancies making communication between process control devices utterly impossible.
As seen in Figure 2, signal noise injected onto electrical communication will add or detract from the expected signal value. In an industrial situation where vital processes are automatically controlled based on the measurement of that signal, any variation can lead to unpredictable and potentially damaging results.
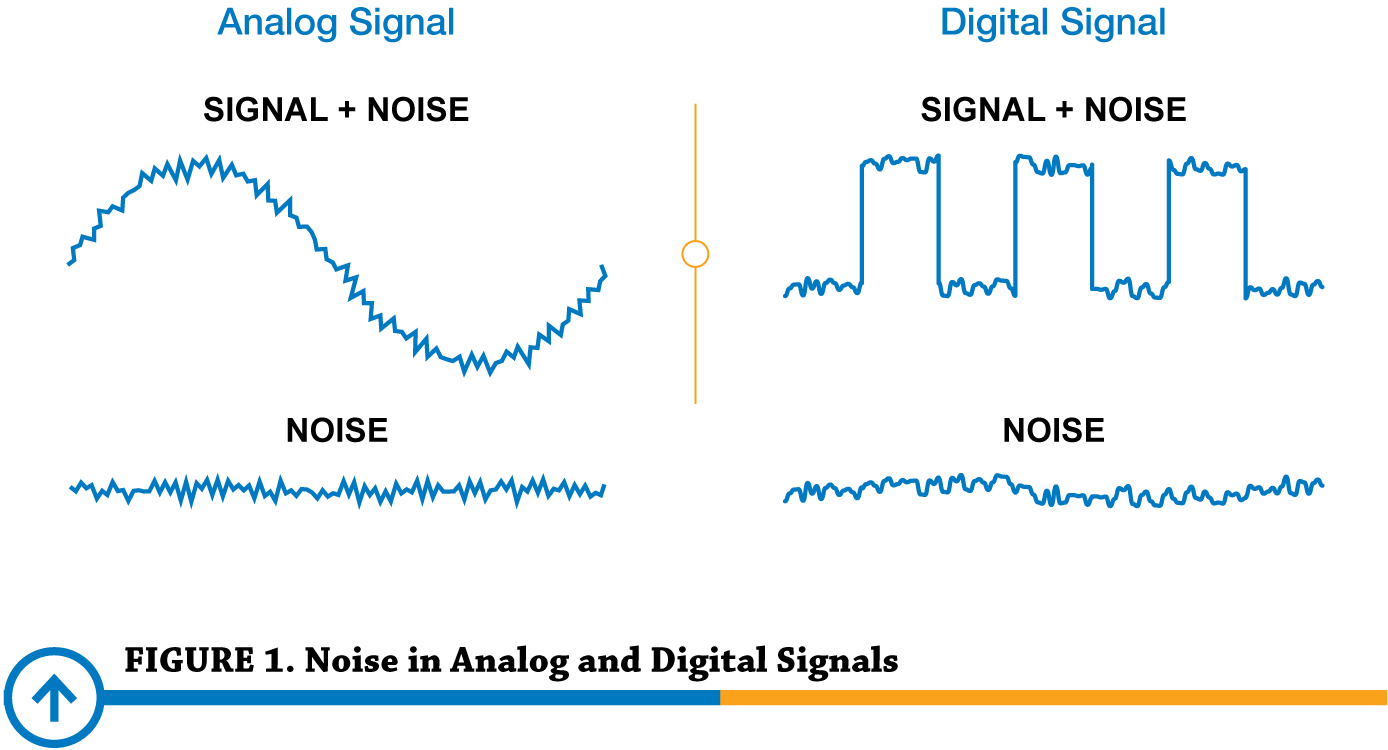
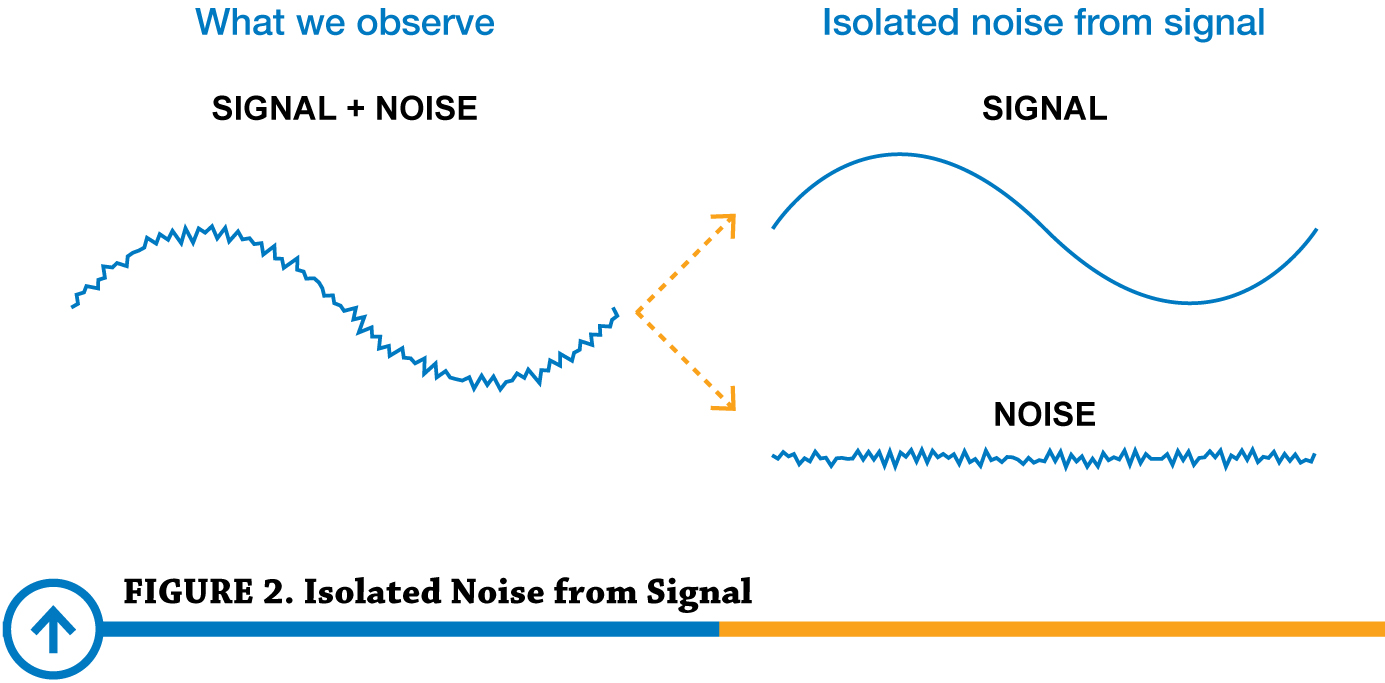
COMMON CAUSES OF SIGNAL NOISE
Noise injection can occur anywhere in the system and at any physical location in which the network is exposed. It can be the result of various factors at any location on the network. It may seem a daunting task to troubleshoot signal noise; nonetheless, there are some causes that are more common than others. These common causes account for the vast majority of signal noise interfering with process control networks.

As discussed in the previous issue of The Current Quandary, ground loops inject additional current onto the signal loop via a voltage differential between two grounding locations in a multi-ground system. This and other grounding issues can lead to an influx of signal noise on an otherwise functional network.

Poorly wired networks, such as those not utilizing shielded twisted-pair and conduit, are more susceptible to ambient electrical noise.

Poorly designed electronic circuitry within devices, which does not provide adequate shielding against internal and external sources of noise, will also be more likely to have signal issues.

Devices or wires placed in close proximity to electrical equipment that generates strong magnetic fields, such as generators, motors, or power lines, can pick up some of that interference, which can contribute to fluctuations in communications signals

Long segments of wire (especially unshielded wire) essentially act as antennae; they pick up radio waves and convert them to electrical signals, contributing to additional noise in the system.
PROBLEMS ASSOCIATED WITH SIGNAL NOISE

The most common and obvious problem caused by signal noise is the distortion of the process signal, causing incorrect interpretation or display of a process condition by the equipment. The addition to and/or subtraction from the process signal translates into an incorrect process variable. To put this into context, see the example in Figure 3 below.

Though uncommon, extreme signal noise can lead to an apparent loss of signal. Most modern electronic equipment have built in noise filtering. However, in extremely noisy environments, this filter will not be enough, which can lead to the equipment not receiving a signal and no communication taking place at all.

In the example discussed in Figure 3, each device on the network is functioning exactly as intended; however, the signal noise caused a miscommunication between devices. Consequently the tank remained empty. A system experiencing signal noise fluctuations could inadvertently turn relays and alarms on / off at irregular intervals because the noisy signals are being misunderstood. A situation like this results in the improper control of an industrial process.


A radar level transmitter is measuring tank liquid level. It outputs a 4-20 mA signal (4 mA when empty and 20 mA when full) to a mechanical relay that when triggered at 4.5 mA, activates a pump to begin filling the tank.

The tank empties and the transmitter outputs a 4 mA signal but, because of extreme signal noise, the relay receives a 5 mA signal and never triggers or activates the pump. The tank remains empty and the process grinds to a halt.
BEST PRACTICES
As with all industrial process control connection problems, it is far easier to follow some simple best practices while planning, designing, and installing process control devices than it is trying to troubleshoot problems with a system after it has become operational. Successful planning can save hundreds of man-hours and untold frustration when it comes to preventing signal noise from interfering with the system.
When it comes to preventing signal noise, the smaller a signal is the more susceptible to noise it is. Low-level signals such as the pulse signal from a magnetic pickup flowmeter or the millivolt output of a thermocouple are highly susceptible to ambient noise. Any amount of noise injected onto these types of systems is bound to have some effect on the signal being transmitted.
Though it may be tempting to simply extend the wires from these devices to connect them to display or control devices, it is highly recommended that a transmitter or conditioner be used to amplify the signal before sending it over any length of wire. This amplified signal will be able to sustain greater quantities of noise before its intended value begins to be muddled. A more effective way to avoid noise, however, is to covert the analog signal to a digital signal instead of amplifying it. As shown in Figure 4, digital signals, with their set of discrete bits, are far more immune to noise than analog.

If a system needs to be installed in an area prone to electrical noise, the installer must plan on using software or hardware noise filters, which are often included in modern process control devices. Look in the device's instruction
manual to ensure noise filters are available. An in depth understanding of the installation's environment and devices can save time and frustration.
As the saying goes, no plan ever survives first contact with the enemy. However, installers must make sure not to let unforeseen environmental or device limitations hinder the installation process or allow for future troubleshooting nightmares. Taking shortcuts to overcome installation challenges might be tempting for the short-term, but in the future that decision will come at a cost.
Installers should always use shielded twisted-pair wire to connect the components of the system. Common mode noise, or noise that is shared between the two wires of the twistedpair, is more easily filtered out than noise that is only present on one wire. Also, though it may seem convenient to run the signal lines through the same conduit as power lines, this should always be avoided. The noise from those 120 or 240 V lines can easily make its way onto the signal lines.
Wires should also be kept away from any equipment that produces magnetic fields, such as motors, transformers, or large relays with inductive loads. Wires connecting different circuits should be installed perpendicular to one another as parallel lines are more likely to exchange noise. Wires should also be kept as short as possible to avoid acting as antennae.
Wiring must always be installed with the intention of avoiding ground loops. This is done by only using a single point of ground for all of the devices present on the network. If multiple devices on the network require grounding, make certain to run the same ground source throughout the entire system on shielded cable.
Keeping these simple best practices in mind throughout the installation process will help to ensure that your implementation takes signal noise into consideration as much as the original planning stages. If the installer of the setup shown in Figure 3 had been following best practices during planning and installation, they would have known that AC power lines should always be isolated from 4-20 mA signal lines by running it along shielded cables inside independent conduit.
SUMMARY
Signal noise is an issue that all industrial facilities experience by virtue of having electrical equipment running. Signal noise becomes a problem for these facilities when it interferes with process signals being conveyed between devices. This can lead to inaccurate communication of critical process variables that can hinder or even halt process control systems. Following some simple best practices while planning and installing your process control solution can help to keep the communication flowing and eliminate the current quandary.
If you have an idea for a future topic to be featured in The Current Quandary, please contact Precision Digital at [email protected]
by Simon Paonessa - Technical Writer, Precision Digital Corporation